在切削加工中,为了最大限度地提高加工质量和重复精度,必须正确地选择和确定合适的刀具,对于一些具有挑战性的高难度加工,刀具的选择尤其重要。
高速刀具路径
CAD/CAM 系统通过在高速摆线刀具路径中精确控制吃刀弧长,而获得极高的切削精度。当铣刀切入转角或切入其它复杂几何形状时,吃刀量也不会增大。为了充分利用这种技术进步,刀具制造商设计开发了先进的小直径铣刀。小直径铣刀通过采用高速刀具路径,能在单位时间内切除更多工件材料,获得更高的金属去除率。
在加工时,刀具与工件表面接触过多,容易导致刀具很快失效,一种有效的经验法则是:使用直径约为工件最窄部位尺寸1/2 的铣刀。当铣刀半径小于工件最窄部位尺寸时,刀具就有左右移动的空间,并能获得最小的吃刀角度。铣刀可以采用更多的切削刃和更高的进给率。此外,采用直径为工件最窄部位尺寸1/2 的铣刀时,可以保持较小的吃刀角度,且在刀具转向时也不会增大。
机床刚度也有助于确定可使用刀具的尺寸。例如,在40 锥度的机床上进行切削加工时,铣刀直径通常应< 12.7mm。而使用直径较大的铣刀会产生可能超过机床承受能力的较大切削力,导致颤振、变形、表面光洁度变差和刀具寿命缩短。
采用较新的高速刀具路径时,铣刀在转角处发出的声音与直线切削时并无二致。铣刀在切削过程中所发出的声音都相同,表明其未受到大的热冲击和机械冲击。铣刀在每次转向或切入转角时都发出尖啸声,则表明可能需要减小铣刀直径尺寸,以减小吃刀角度。切削发出的声音保持不变,表明铣刀承受的切削压力均匀一致,并未随着工件几何形状的变化而上下波动,这是因为其吃刀角度始终保持恒定。
铣削狭小部位
大进给铣刀适合狭小部位的铣削加工,可以产生切屑减薄效应,使其能以更高的进给率进行铣削。
在螺旋铣孔和铣削肋板的加工中,刀具不可避免地会与加工表面产生较多接触,而采用大进给铣刀可以最大限度地减少与工件的表面接触,从而减少切削热和刀具变形
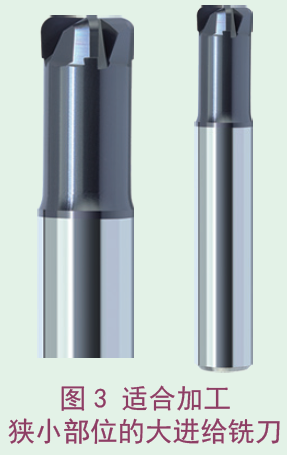
在这两种加工中,大进给铣刀切削时通常处于半封闭状态,因此,最大径向走刀步距应为铣刀直径的25%,而每次走刀的最大Z 向切深应为铣刀直径的2%。在螺旋铣孔中,当铣刀以螺旋刀轨切入工件时,螺旋切入角为2°~ 3°,直至达到铣刀直径2%的Z 向切深。
若大进给铣刀切削时处于开放状态,其径向走刀步距取决于工件材料的硬度。铣削硬度为HRC30-50 的工件材料时,最大径向走刀步距应为铣刀直径的5%;当材料硬度高于HRC50 时,最大径向走刀步距和每次走刀的最大Z 向切深均为铣刀直径的2%。
铣削直壁在铣削加工带平肋板或直壁时,使用圆弧铣刀效果最好。4-6 刃的圆弧铣刀尤其适合对带直壁或非常开阔的部位进行仿形铣削。铣刀的刃数越多,可采用的进给率越大。不过,加工编程人员仍需尽可能减少刀具与工件的表面接触,并采用较小的径向切宽。在刚性较差的机床上加工时,采用直径较小的铣刀比较有利,小直径铣刀可减少与工件的表面接触。
多刃圆弧铣刀的走刀步距和切削深度与大进给铣刀相同。可采用摆线刀具路径对淬硬材料进行切槽加工。确保铣刀直径约为槽宽的50%,使铣刀具有足够的移动空间,并确保吃刀角度不会增大和产生过多的切削热。
适合特定加工的最佳刀具不仅取决于被切削材料,还取决于所采用的切削类型和铣削方法。通过优化刀具、切削速度、进给率和加工编程技巧,就能以更低的加工成本,更快、更好地生产零部件。